Custom CNC Machining Manufacturer: Elevating Your Manufacturing Capabilities
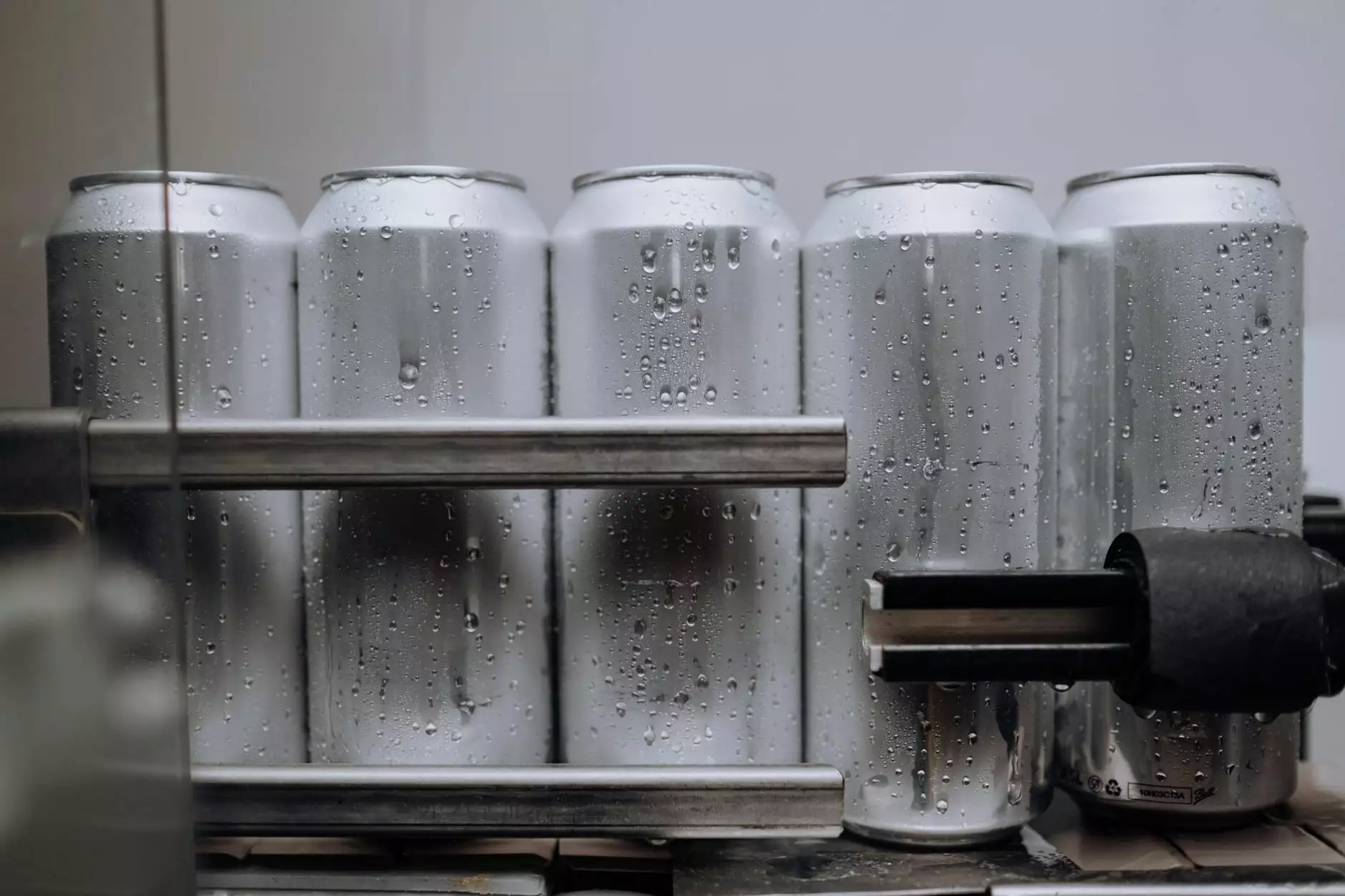
The evolution of manufacturing in the modern era has been nothing short of revolutionary. At the heart of this transformation lies the role of the custom CNC machining manufacturer, providing businesses with the tools they need to thrive in a competitive landscape. In this comprehensive article, we will delve into the critical aspects of custom CNC machining, its benefits, applications, and how partnering with a dedicated manufacturer can elevate your production capabilities to new heights.
Understanding CNC Machining
CNC, or Computer Numerical Control, is a technology that automates the control of machining tools via a computer. This automation allows for precise manufacturing processes, resulting in high-quality parts that meet exact specifications. The components are created by precisely removing material from a solid block, which can be anything from metal to plastic, based on the requirements of the project.
The Role of Custom CNC Machining Manufacturers
Custom CNC machining manufacturers specialize in producing bespoke parts tailored to the unique needs of their clients. Unlike off-the-shelf solutions, custom machining allows for:
- Tailored Specifications: Parts can be designed to meet exact dimensions and tolerances.
- Material Versatility: Manufacturers can work with a wide range of materials, including aluminum, steel, plastics, and composites.
- Innovative Designs: The use of CAD (Computer-Aided Design) software enables complex geometries that would be impossible with traditional machining methods.
- Reduced Waste: CNC machining optimizes material usage, which not only saves costs but also minimizes environmental impact.
Benefits of Partnering with a Custom CNC Machining Manufacturer
1. Enhanced Precision and Quality Control
One of the most significant advantages of utilizing a custom CNC machining manufacturer is the level of precision achieved. CNC machines are capable of producing parts with tolerances as tight as ±0.001 inches. This precision ensures that the parts manufactured consistently meet quality standards, which is paramount for industries such as aerospace, automotive, and medical devices.
2. Increased Efficiency in Production
Custom CNC machining allows for rapid prototyping and production. Once a design has been finalized, CNC machines can produce parts in large quantities with minimal human intervention, significantly speeding up the production process. This efficiency translates into faster time-to-market for products, giving businesses a competitive edge.
3. Flexibility to Adapt Designs
In a dynamic market, flexibility is key. Custom CNC machining manufacturers can easily adapt to changes in design or material specifications. Whether you need to tweak an existing part or develop an entirely new component, these manufacturers can accommodate changes seamlessly, ensuring that your project stays on track.
4. Cost-Effectiveness
While there may be an initial investment in custom CNC machining, the long-term savings can be significant. By reducing material waste, minimizing labor costs, and speeding up production times, businesses can achieve a favorable return on investment. Moreover, the enhanced quality and durability of custom parts can lead to lower failure rates and decreased maintenance costs.
Applications of Custom CNC Machining
The versatility of custom CNC machining makes it applicable across various industries. Here are some prominent applications:
- Aerospace: Components for aircraft and spacecraft that require stringent safety standards and precision.
- Automotive: Custom parts for vehicles, including engine components, brackets, and custom tooling.
- Medical: Surgical instruments and implants tailored to specific medical needs and patient requirements.
- Electronics: Enclosures, heat sinks, and custom mounting solutions for electronic devices.
- Manufacturing: Fixtures and jigs designed for specific production lines to enhance assembly efficiency.
The Process of Custom CNC Machining
Understanding the process of custom CNC machining is essential for businesses looking to take advantage of this technology. Below is a detailed overview of the common steps involved:
1. Design Phase
The journey begins with the design phase, where clients collaborate with engineers to develop precise models using CAD software. This step includes outlining the dimensions, materials, and functionalities required for the part. Effective communication during this phase is crucial to ensure the end product aligns with expectations.
2. Material Selection
The choice of material is critical as it affects the properties of the final product. A custom CNC machining manufacturer can help guide you through options based on factors such as strength, weight, corrosion resistance, and cost.
3. Machining Setup
Once the design is finalized and materials selected, the CNC machine is set up. This setup includes installing the cutting tools, loading the material, and programming the machine with the specifications provided by the design phase.
4. Machining Process
During the machining process, the CNC machine operates automatically based on the programmed instructions. It precisely removes material from the workpiece to create the desired shape. Throughout this process, quality control checks are performed to ensure specifications are met.
5. Post-Processing
After the initial machining, parts may require additional post-processing steps to achieve the desired finish. This can include sanding, polishing, or even surface treatments to enhance properties such as durability or visual appeal.
6. Quality Inspection
Finally, each part goes through a rigorous quality inspection process, which may include dimensional checks, functionality tests, and material evaluations to ensure it meets all specifications.
Choosing the Right Custom CNC Machining Manufacturer
Selecting the right custom CNC machining manufacturer can be an overwhelming task, especially with the sheer number of options available. Here are some key factors to consider:
- Experience and Expertise: Look for manufacturers with a proven track record and experience in your specific industry.
- Technology and Equipment: Ensure the manufacturer uses state-of-the-art CNC machining equipment and software to guarantee quality.
- Quality Standards: Check if they adhere to recognized quality standards such as ISO certifications.
- Customer Service: A responsive customer service team is vital for collaboration throughout the project, from design to production.
- Flexibility: The ability to adapt to changes and unique requirements is essential for successful project completion.
Conclusion
In conclusion, partnering with a custom CNC machining manufacturer can provide unparalleled advantages for businesses looking to enhance their manufacturing capabilities. From ensuring precision and quality to offering cost-effectiveness and adaptability in design, the benefits are extensive. Whether you operate in aerospace, automotive, medical, or any other industry, leveraging the expertise and technology of a custom CNC machining manufacturer is a strategic move toward achieving long-term success.
By integrating custom CNC machining into your manufacturing processes, you are not just improving efficiency; you're elevating your entire business model. Explore the possibilities today, and take the first step toward a future defined by precision, innovation, and excellence in manufacturing.