Maximize Your Production with Silicone Membrane for Vacuum Press
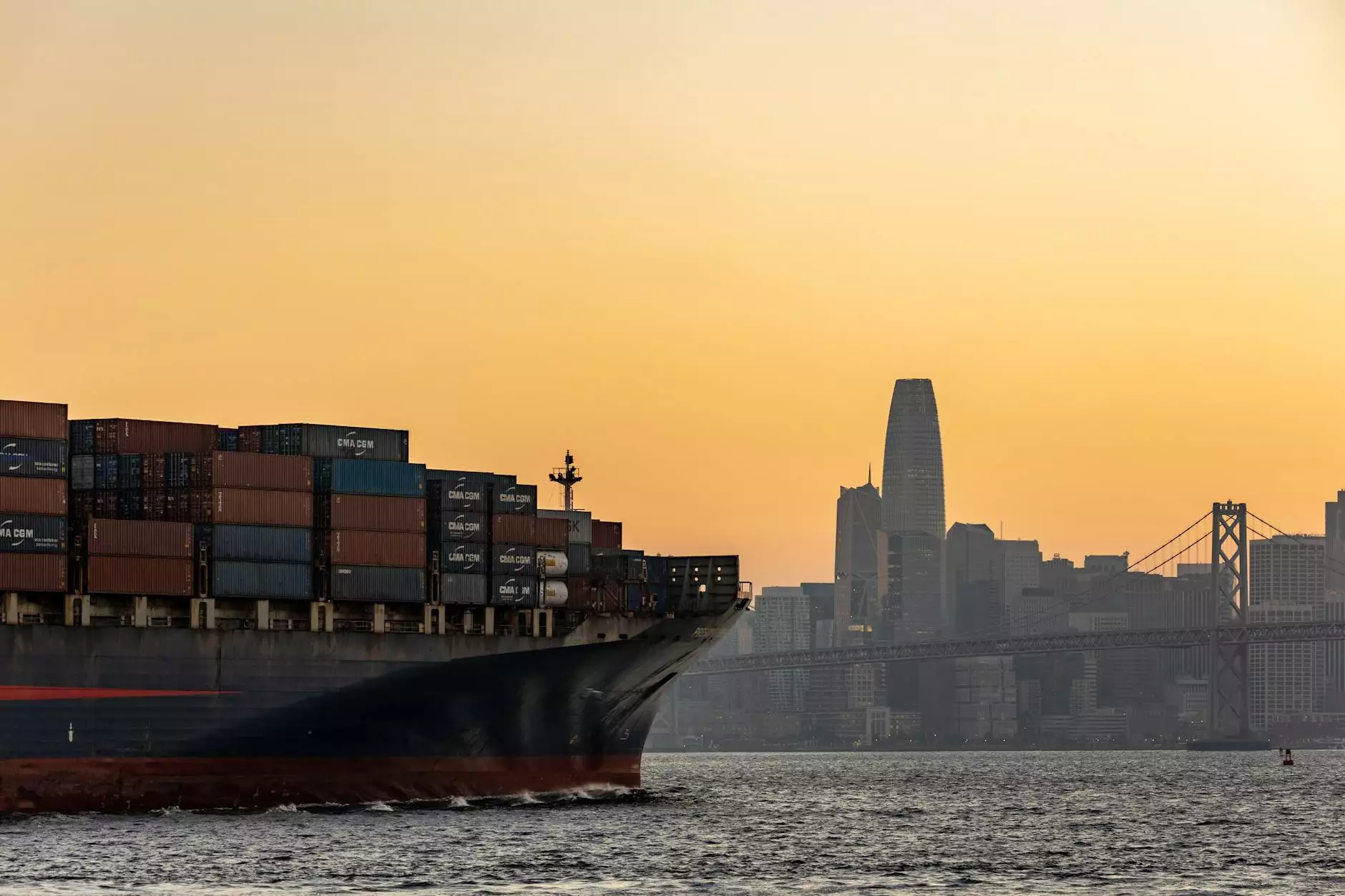
In the modern landscape of manufacturing and production, efficiency and quality are no longer optional; they are essential. One of the critical components that contribute to achieving these goals is the silicone membrane for vacuum press. This article delves into why silicone membranes are indispensable in vacuum pressing and how they can enhance your operational capabilities.
Understanding Silicone Membranes
Silicone membranes are highly flexible, durable, and resistant to a variety of chemicals and temperatures. These characteristics make them an ideal choice for use in vacuum presses, where they exert the necessary pressure on materials to ensure consistent results. In a vacuum system, the silicone membrane acts as a barrier that conforms to the shape of the substrate, ensuring an even distribution of force.
Key Properties of Silicone Membranes
- Heat Resistance: Silicone can withstand high temperatures without losing structural integrity, making it perfect for various manufacturing processes.
- Flexibility: A silicone membrane can conform to various shapes and surfaces, ensuring optimal contact.
- Chemical Resistance: They resist oils, solvents, and other harsh chemicals that could degrade other types of materials.
- Durability: Silicone membranes have an extended lifespan compared to rubber membranes, reducing replacement costs and downtime.
Applications of Silicone Membranes in Vacuum Presses
Silicone membranes are versatile and can be employed in various industries. The following are a few notable applications:
1. Woodworking Industry
In woodworking, silicone membranes are used in vacuum presses to laminate surfaces, bend wood into desired shapes, and apply finishes evenly. The ability for silicone to withstand heat and moisture makes it a favored choice among woodworkers.
2. Aerospace Engineering
Aerospace components often require precision and a lightweight material, making silicone membranes ideal due to their strength and lightness. These membranes ensure that components are accurately shaped and free from defects.
3. Automotive Manufacturing
In the automotive sector, silicone membranes are employed in the production of composite materials. This includes parts such as dashboards and other interior elements, where high-quality finishes and robustness are essential.
Benefits of Using Silicone Membranes in Vacuum Presses
The use of silicone membranes demonstrates numerous benefits that impact production positively:
1. Improved Product Quality
Silicone membranes provide a uniform application of pressure, leading to higher-quality finishes and reduced defects in manufactured goods.
2. Cost Efficiency
While the initial investment may be higher, the longevity and durability of silicone membranes mean savings over time, minimizing replacement and maintenance costs.
3. Enhanced Performance
Silicone membranes allow for consistent performance even under challenging conditions, letting manufacturers maintain productivity.
4. Versatility Across Applications
From wood to composites, silicone membranes adapt well to several materials, making them a multi-functional investment for businesses.
Choosing the Right Silicone Membrane for Your Vacuum Press
Selecting the right silicone membrane for vacuum press can significantly impact your production efficiency. Here are essential factors to consider:
1. Thickness of Membrane
The thickness of the silicone membrane will affect its flexibility and durability. Thicker membranes may offer more durability but could lack the flexibility needed for specific applications.
2. Temperature Ratings
Ensure that the silicone membrane can withstand the temperatures it will encounter during the manufacturing process. Each application may require different temperature tolerances.
3. Chemical Compatibility
Consider the chemicals the membrane will be exposed to during production. A membrane with high chemical resistance will last longer and perform better.
4. Manufacturer’s Reputation
Buy from a reputable supplier like Vacuum-Presses.com that offers high-quality silicone membranes backed by strong customer service and warranty options.
Conclusion
Investing in a silicone membrane for vacuum press will undoubtedly improve your production efficiency and product quality. By understanding the properties, applications, and selection criteria for these membranes, businesses can position themselves to maximize their output. The versatile and durable nature of silicone membranes supports a range of industries, making them a wise investment for any manufacturer seeking to enhance their operational capabilities.
For more information about silicone membranes and to view our extensive range of products, visit Vacuum-Presses.com.
Frequently Asked Questions (FAQs)
1. How long do silicone membranes last?
The lifespan of silicone membranes can vary based on usage and conditions, but with proper care, they can last several years.
2. Can I use silicone membranes for materials other than wood?
Absolutely! Silicone membranes are suitable for various materials, including composites, plastics, and metals.
3. Do silicone membranes require special care?
Generally, silicone membranes should be cleaned with mild soap and water. Avoid using harsh chemicals that could degrade the material.
4. What is the maximum temperature that silicone membranes can withstand?
Silicone membranes can typically withstand temperatures up to 400°F (204°C), but this may vary based on the specific product.
5. Where can I purchase high-quality silicone membranes?
You can purchase silicone membranes from reliable suppliers such as Vacuum-Presses.com, where a wide range of options is available.