Understanding Oil Seal Manufacture in Diesel Engine Parts
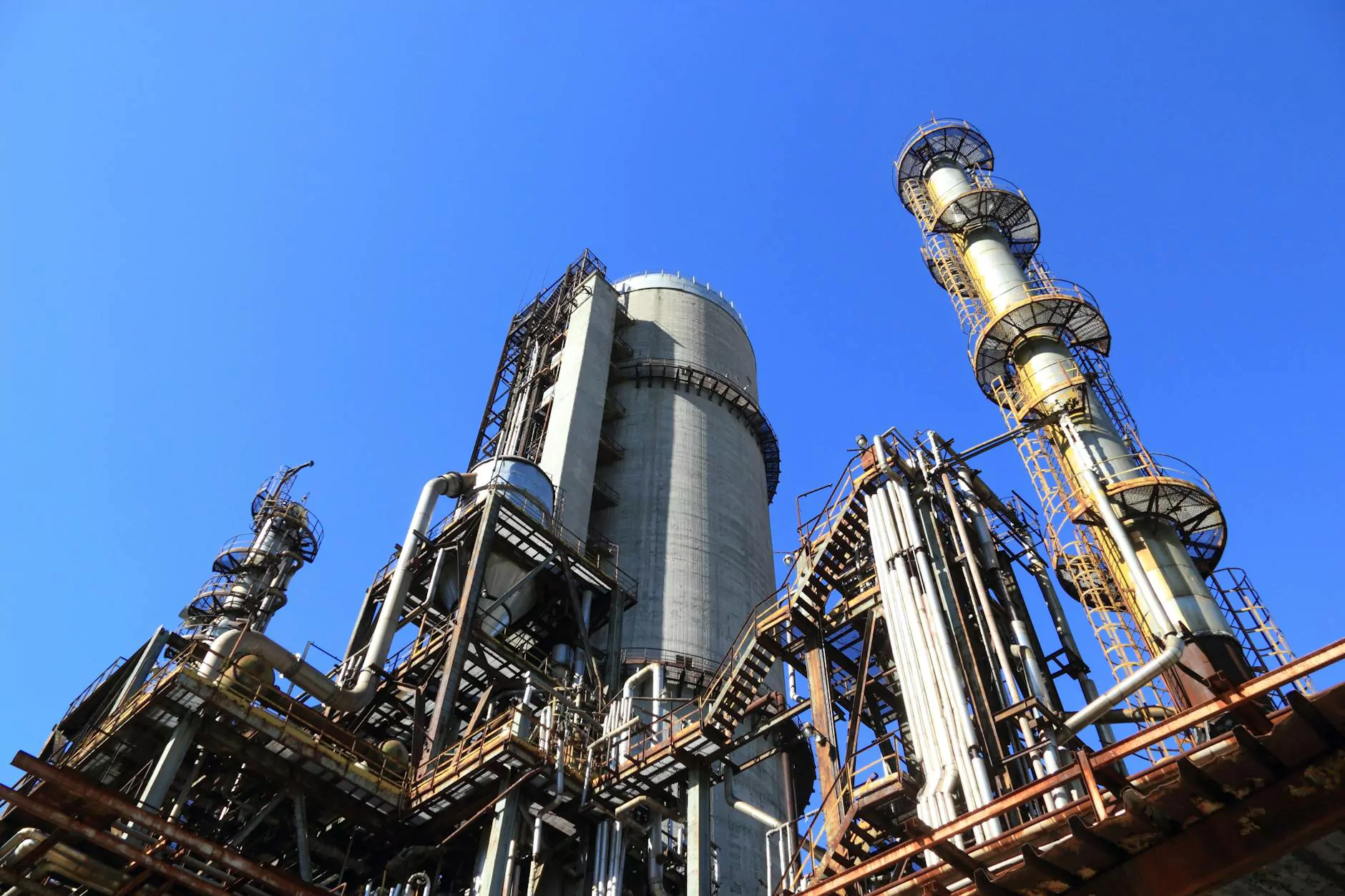
Oil seal manufacture plays a pivotal role in the overall performance and longevity of diesel engines. Diesel engines are known for their robustness, but they are complex machines that require a multitude of components, including seals, to function optimally. In this article, we will delve deep into the world of oil seals, their significance, and how they are manufactured, especially in the realm of diesel engine parts.
The Basics of Oil Seals
Oil seals are critical components designed to retain lubrication while preventing the ingress of contaminants. They are used in various applications, but in the context of diesel engines, their functionality is paramount. Key characteristics include:
- Material Composition: Oil seals are often made from elastomeric materials, such as nitrile rubber, which offer excellent sealing properties.
- Design: The design can vary significantly based on the application, with different shapes and sizes to fit various engine designs.
- Function: They primarily prevent oil leakage from the engine, contributing to better efficiency and reduced emissions.
Importance of Quality Oil Seal Manufacture
High-quality oil seals are essential for maintaining the efficient operation of diesel engines. The integral role they play includes:
- Preventing Oil Leakage: Oil leaks can cause significant damage to the engine, leading to costly repairs and downtime.
- Maintaining Lubrication: Proper lubrication is essential for reducing friction between moving parts, thus prolonging engine life.
- Enhancing Fuel Efficiency: An effective seal ensures that oil stays where it should, optimizing engine performance and ensuring better fuel economy.
- Reducing Emissions: Well-manufactured seals help in lowering harmful emissions by preventing oil leakage.
The Manufacturing Process of Oil Seals
The oil seal manufacture process involves several critical stages to ensure the final product meets the stringent standards required by diesel engine applications. Here’s a detailed overview of this process:
1. Material Selection
The choice of material is crucial for the performance of oil seals. Manufacturers typically select high-quality elastomeric materials that can withstand heat, pressure, and exposure to oil. Common materials include:
- Nitrile Rubber (NBR): Known for its excellent oil resistance and durability.
- Fluorocarbon Rubber (FKM): Resistant to high temperatures and aggressive chemicals.
- Silicone Rubber: Offers superior flexibility and temperature resistance.
2. Design and Engineering
After the material is selected, the design phase begins. Engineers use advanced CAD software to create precise designs tailored to specific engine requirements. Key factors in the design include:
- Dimensions: Size and shape of the seal to ensure a perfect fit.
- Structural Integrity: Design must withstand operating pressures and temperatures without failing.
3. Manufacturing Techniques
Oil seals can be manufactured using various techniques, depending on material properties and design specifications. Common methods include:
- Injection Molding: A prevalent method for creating complex shapes with high precision.
- Compression Molding: Suitable for large seals, allowing for uniform thickness and density.
- Transfer Molding: Combines elements of both injection and compression molding for customized designs.
4. Quality Control
Once the seals are produced, rigorous quality control tests are conducted to ensure they meet industry standards. These tests may involve:
- Dimensional Checks: Verifying measurements against specifications.
- Performance Testing: Assessing how seals perform under real-world conditions.
- Durability Testing: Evaluating long-term performance under simulated operational environments.
Supplier Considerations for Oil Seals
Choosing the right supplier for oil seals is crucial. When evaluating suppliers, consider the following:
- Experience: Look for a supplier with a proven track record in oil seal manufacture.
- Quality Assurance: Ensure they adhere to ISO or other international quality standards.
- Customer Support: Reliable suppliers should offer excellent customer service and support.
- Product Range: A diverse range of products can indicate expertise and capacity to meet varying needs.
Client-Diesel: Your Trusted Partner in Diesel Engine Parts
At client-diesel.com, we pride ourselves on being leading suppliers of diesel engine parts, including top-quality oil seals. Our commitment to quality, engineering excellence, and customer satisfaction sets us apart. Here are some reasons why you should choose us:
- Comprehensive Product Offerings: We provide a wide range of diesel engine parts, ensuring all your needs are met.
- Expertise: Our team has extensive experience in the industry, enabling us to provide valuable insights and support.
- Competitive Pricing: We strive to offer the best prices without compromising on quality.
- Timely Delivery: We understand the importance of timely deliveries in keeping your operations running smoothly.
Conclusion
Efficient oil seal manufacture is essential for the proper functioning of diesel engines. With the right materials, advanced manufacturing processes, and rigorous quality control, high-quality oil seals can significantly improve engine performance, reduce downtime, and extend the service life of engines. At client-diesel.com, we are dedicated to providing exceptional products and services to meet your diesel engine part needs. Trust us for all your oil seal requirements and experience unparalleled service.